What is Non-Destructive Testing?
Non-Destructive Testing (NDT), is essentially any form of testing that can be performed without causing irreversible change. This testing can include dimensional inspection, PMI (Positive Material Identification), Ultrasonic Inspection and crack detection via Mag Particle (MT) or Dye Penetrant (PT), all of which we are trained and certified to do here at Hi-Tech Compressor.
But what are the purposes?
The uses for these testing methods overlap many of the processes we do here on a day to day basis. These can range from dimensional inspection of a newly manufactured run of parts from our CNC department, identification of the base material of a compressor rod prior to thermal spray or checking a cast iron valve seat for cracks before reconditioning. The focal point is verification of any unknown detail that may compromise a parts' integrity or cause a part to not function properly.
What Equipment is necessary?
As with any specialized process, having the right tools is essential to obtaining the best results. Below is a brief overview of the specialized equipment we use here at Hi-Tech for NDT.
-
Niton XL3 PMI Gun
This gun uses an X-Ray beam to permeate the surface of a material, excite molecules and read from that the composition of the material on the atomic level. From this, the gun not only identifies the atoms but also calculates the proportions and uses a chart to classify the material type (e.g. 4140 Steel, 6061 Aluminum, etc.)
Above: An inspector (Dave; CAD/CAM/ CNC Supervisor) is using the Niton XRF gun to identify a parts material for reverse engineering.
-
Olympus 45 MG Ultrasonic Thickness Tester
An ultrasonic thickness tester is essentially a precision stopwatch that uses sound waves to measure distance. The principle is simple. Pass a sound wave through a material.When it hits air it will return back giving the processor an elapsed time. But time is only one-half of the equation, where the other half is speed. Every material has a velocity at which sound passes through, giving us all the information necessary to calculate thickness from one side of an object without needing access to the other.
Above: An inspector is taking thickness readings on a pump casing prior to disassembly in order to diagnose a leak. Not shown in this picture, our XRF gun is used prior to this step to determine material composition allowing to fine tune our thickness meter.
-
Crack Detection
Officially called a “discontinuity”, a crack is a rather simple flaw to detect and doesn’t necessarily require special tools. What is required is a fundamental understanding of how a crack will propagate in a particular part and how to find it. To accomplish this, our inspectors have level 2 certification in both the PT & MT methods (briefly outlined below):
-
Visible Solvent Removed Dye Penetrant (PT) - Also known as “Three cans and a rag”, this method is the most common and widely used. The key benefits are portability and having the ability to test non-ferrous materials. The main limitation is the inability to find a sub-surface flaw.
-
Visible Mag Particle (MT) - Mag particle can be broken down into six groups, but the concept remains the same. Magnetize a part and locate where the magnetic field (flux) leaks out. This will typically lead to an indication of a surface (or mildly subsurface; 1/4”) discontinuity. The crack has been located.
Above: A side by side comparison of the two before mentioned methods. On the left is MT, using the Wet fluorescent method. On the right is the visible solvent removed method representing PT. Both methods require attention to detail regarding penetrant choice, dwell time of components and lighting (intensity and residual)
-
Hydro Testing
Hydro testing also known as hydrostatic testing is performed to detect cracks and leaks in the part. Tests can be done on certain parts such as cylinders, compressor cylinders, cylinder heads, and power cylinder heads. The test will also indicate the parts overall strength. This test is visually detected through leaks produced by the water that can contain a colorant. This test will ensure the parts safe and reliable performance during its operating lifetime.
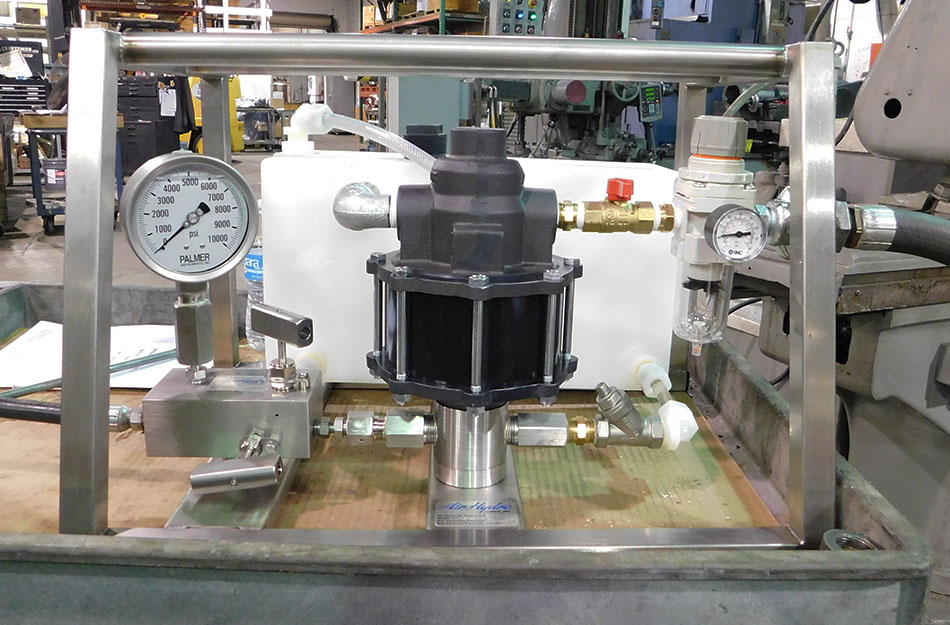