Posted on Wednesday, December 22, 2021
By:
Hi-Tech Compressor & Pump Products, Inc.
Categories:
Services
“With our new laser alignment equipment, we get extremely accurate and consistent results from setup to setup and from person to person, time after time.” -Don Weidemann, Director of Quality, Hi-Tech Compressor and Pump Products
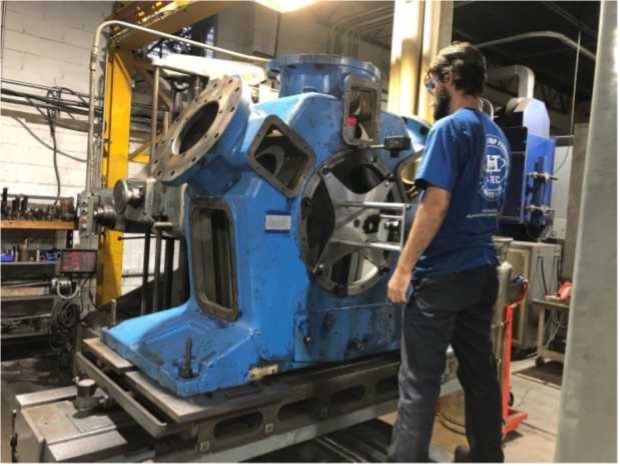
Hi-Tech's Quality Inspector Phil Sofia checks compressor housing with our laser system
Using Lasers to Nail Critical QC Checks on Compressors
Hi-Tech Compressor and Pump Products, based in Tullytown, Pennsylvania, had just taken on a challenging compressor reconditioning project and was trying to sort out how to QC the alignment. Our company specializes in refurbishing reciprocating compressors and industrial pumps, and has a reputation for expert, responsive service as well as high quality work.
Don Weidemann, Hi-Tech's Director of Quality, had to be certain the tolerances of the compressor bearing bores were on spec, but his customized dial indicator setup was not providing consistent results. Our reputation was on the line, the tolerances were very tight and his measurements had to be repeatable and reliable. After careful research, he found the answer in a new laser alignment system made by Hamar Laser Instruments.
The rewards:
- The high Gage R&R (Repeatability & Reproducibility) of the laser equipment gave Hi-Tech “absolute confidence” in the accuracy of its work; quick and intuitive setup made it easy for shop floor techs to use.
- The Hi-Tech team got an enthusiastic “high-five” for the compressor reconditioning job and quickly got more business from the customer.
- Hi-Tech has added laser alignment to its already robust suite of capabilities and expects to win additional business as a result.
Large Multi-Throw Frames
Founded in 1999, Hi-Tech serves customers in many industries, including Oil & Gas, which makes wide use of reciprocating compressors. Owner Todd Pollazzi said Hi-Tech stands out for its ability to respond much faster than large OEMs and similar companies, with little red tape, to address customers' needs - a small, nimble company with big capabilities, including full-service machining and in-house thermal spray.
Hi-Tech's Management Team (L to R): Operations Director Adam Cojocaru, Director of Quality Don Weidemann & President Todd Pollazzi
Hi-Tech's customer for the reconditioning job at the heart of this case study is a large service company that specializes in servicing reciprocating compressors used throughout the world in P.E.T. bottle blowing applications. These units' multi-throw frames are very expensive to replace, so being able to repair the bearing bores to better-than-original condition with thermal spray or sleeves represents a huge savings for the owner. The tolerances are very tight and maintaining perpendicularity is essential.
“Our customer for this job knew us for repairing their other reciprocating wear parts,” Pollazzi said. “During a tour of our shop we showed them our metal spray capabilities, and they asked us to repair their worn frames. Our customer had tried to repair the frames, but struggled to maintain the needed sizes and perpendicularity.”
Extremely Tight Tolerances
According to Weidemann, the reconditioning job that others would not or could not tackle effectively was a great fit for Hi-Tech. “While our company is only 22 years old, our founders have extensive experience with compressors,” he explained. “For a smaller company we have broad in-house capabilities; this includes CNC and large machining capabilities, nondestructive testing capabilities, and multiple types of thermal spray. We can spray stainless steel, carbide, ceramic, aluminum and bronze, and we have an extremely impressive ability to inspect our product.”
Weidemann explained that the bearing bores are especially critical on these compressor designs, and this is why the manufacturer assigned extremely tight tolerances for them. “They have three in-line bearings on a single shaft so if there is any misalignment, the techs can feel it when they slide the parts together,” he said. “Because of our broad knowledge, we were able to take on the job and develop a process for reconditioning the bores that has worked very well.”
Although well-equipped for Quality Control, Hi-Tech did not have equipment that would let Weidemann check the compressors with sufficient confidence. Initially, he designed a custom fixture using dial indicators, but the extended length of the fixture and indicator arms made it heavy and sensitive to angular movement, which made the readings inconsistent and less accurate. The same limitations with dial indicators caused us to struggle with accurately aligning the cases in the boring mill. This led to a search for a laser solution instead of a mechanical one.
Measurement Repeatability & Reproducibility
Weidemann said he researched several offerings targeting bore alignment, but this equipment was the first laser he saw that also addressed perpendicularity. “This equipment looked like a promising solution,” he recalled. “This prompted me to contact the manufacturer of the laser equipment. They helped me design and fabricate a fixture to support and center the laser and brought their laser equipment to our facility.”
“We were impressed by the outstanding Gage Repeatability and Reproducibility of the laser alignment system,” Weidemann continued. “While we had been exceeding the compressor manufacturer's tolerances with the dial indicator, it had poor Gage R&R. We would set it up three times and get three slightly different results. With the laser solution we get extremely accurate and consistent results from setup to setup and from person to person, time after time.”
“You don't want your gaging to use more than 10% of your tolerance,” Weidemann explained. “That leaves 90% of your tolerance for machine variation. My inspector and I can set up the laser equipment multiple times and the laser will repeat to within .0002 in. With a .002 in. tolerance that's only 10% of the tolerance being used by the measuring device, and that's an ideal situation!”
Alignment for Machining
In addition to quality checks of the bore alignment, the laser equipment is used to setup the housings in the boring mill. The laser combines an automatically sweeping laser scan plane with a perpendicular laser “plumb” beam for perpendicularity. This allows the alignment process to square the frame to the spindle and then adjust the X and Y spindle coordinates to the precise center of the bores. The frames are aligned initially before rough machining and then the alignment is verified before taking the finish cuts.
Benefits
Hi-Tech's return on investment with the laser equipment is impressive - and not entirely measured in dollars. The gains show up in multiple columns on our ROI spreadsheet: labor savings, greatly enhanced QC and measurement capabilities, longer and more reliable compressor operation, additional customer business and expanded market potential.
Streamlining setup, measuring and machining processes and avoiding costly “do-overs” were important gains. “Each compressor housing takes approximately 80 hours of labor,” Weidemann explained. “By getting them right the first time we save significant warranty and labor costs in not having to repeat parts of the process. With the laser, we and our customers can have absolute confidence in our work.”
The laser is also used to align the housing to the boring mill spindle
In the end, nothing is more valuable than happy customers. Adam Cojocaru, Hi-Tech's Operations Director, was the first to report that the customer was seeing tangible results from Hi-Tech's use of the equipment. “During final assembly, our customer noticed a decrease in difficulty when installing the second and third bearings into the bores and attributed this to improved concentricity of the finished bores,” he said. The satisfied customer quickly shipped additional compressor housings to Hi-Tech for reconditioning.
“Typically, you only hear from a customer if they're not happy,” Weidemann quipped. “They actually called us up to tell us that these are going together great - and by the way we have more that we're going to send you! In the long run, we expect this customer to see longer bearing life due to improved alignment, which is a very important additional benefit.”
Making the most of our success, Hi-Tech is expanding our new capabilities to all current and prospective customers as this can help make their compressors and pumps run longer and more reliably. The bottom line: A bigger piece of the reconditioning market because Hi-Tech can now do what others won't do - or can't do.
Additional Information:
Visit us at
www.hi-techcompressor.com, or call us at 215-547-8800
Tagged:Quality